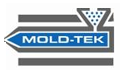
Q & A With
Mr. Laxman J Rao
CMD
What is your take on the unfolding consumption story in India?
We are one of the few players in the organised segment and a leading company in
rigid plastic packaging, specialising in both standard and made to order packaging
solutions for leading brands of paints, lubricants, pharmaceuticals, cosmetics,
FMCG etc.
We cater to the Lubricants used in the Automotive segment and to Paints which is
part of the consumer segment. We derive approx. 35 % of revenue from Lubricants
and 20% from Paints. The purchasing power and the disposable income in the Indian
economy is growing rapidly. Changing lifestyle patterns has shifted consumer preference
towards branded, well packaged and well-presented products, including packaged /ready
to eat food products. In this context, packaging plays a crucial role in the marketability
of a product. Apart from this, we have initiated entry into the Food and FMCG space
by supplying packaging to players in the food industry.
How are you planning to capitalize on this growth?
We are pioneers in bringing in many new concepts like PAILS, In Mould spouts etc., to the Indian packaging arena and now for the first time in India we introduced IN-MOULD LABEL (IML) decoration using ROBOTS to offer world class containers with photographic print quality and hygienic robotic operations. This will fuel faster growth for company’s products considerably.
In addition, the increasing domestic purchasing power is fuelling demand for products like Paints, Lubricants, Food and FMCG products, boosting demand for our products. Our foray into the Food and FMCG space and addition of new clients will help us register strong growth in the top line and bottom line.
India’s FMCG sector is poised to reach USD 43bn by 2013 and USD 74bn by 2018. Within this, the packaging demand will be about USD 2.5bn. These numbers are enough to give an idea about the business opportunity in the FMCG segment.
Having acquired the in-house ability to manufacture moulds, labels and Robots, an advantage no other packaging company can offer, we plan to go full haul into this segment in next few years.
With our unique offering of IML, we are hopeful of acquiring new customers in this particular segment at a rapid pace. Our state-of-art in house tool room with sophisticated Swiss & German machinery to design and produce complex multi cavity moulds gives us further advantage over our competitors, making us confident of successfully leveraging the market opportunity in the Food segment.
Going forward, we expect the FOOD AND FMCG space to contribute significantly to our topline and bottom line, and the traditional clients shifting to in-mould products. Consequently, our revenue mix and profitability is expected to improve to include increasing contribution from this space.
IML, multi location operations for cost efficiency, better reach, sophisticated technology for competitive pricing and ongoing innovation are the few factors that set Mold-tek apart from its competitors, driving the growth in the Company.
What is your production capacity at various plants? What are the plans for expansion?
Present capacity is around 15,000 TPA and is expected cross 20,000 tons by end of April 2012, after the Daman plant expansion.
We have acquired around 3.5 acres land in Daman and are setting up a plant in the area at an investment of Rs. 150mn. The construction of the facility is progressing rapidly and is expected to go into production by April 2012. Post completion, production from the Daman facility will enhance our capacity by more than 30%.
We plan to expand by another 50% next year by setting up plants in two new locations. On the anvil is also a plant outside India, the details of which are being worked out.
We foresee the need to expand capacity by around 40-50% per annum over the next few years.
Strengths:
- First mover advantage in establishing Robots for IML and compatible moulds in India
- No post moulding operation; direct packing from moulding
- State of the art in house tool rooms equipped with sophisticated Swiss and German machinery to design and produce complex molds
- Strategically located manufacturing units for easy accessibility and timely delivery
- Sustained efforts and investments in knowledge-building, training and development has led to an innovation-driven culture